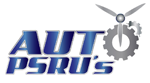
Frequently Asked Questions
PSRU for LS1 Engines:
- Operating Temperature?
- How is the PSRU lubricated?
- What type of oil is recommended?
- How much oil does it hold?
- How does the prop governor work on your PSRU?
- Will my prop governor work with your PSRU?
- Why do you use a centrifugal clutch?
- My old PSRU chatters and jumps around at low engine RPM. Does yours?
- How do you resolve torsional vibrations?
- What about planetary gears in a PSRU?
- Do you test run each Geared Drives PSRU?
- How much horsepower will your PSRU take?
- I have an electric prop. Can I use it with your PSRU?
- Can I use a fixed pitch prop?
PSRU for Subaru:
- Any plans for a Geared Drive PSRU for Mazda?
- more coming soon…
Engine Package Questions:
- Why build a FWF package for the RV-10?
- How much does an LS1 weigh vs. O-540?
- How does the engine RPM compare to the IO-540?
- Thoughts on your engine packages on P-51 replicas?
- How about Chevrolet engines for Twins?
- How about Diesel engines in aircraft?
- What cooling setup do you recommend for your engine packages?
- What about baffling?
- Did you say close off the front air inlets?
- What about drag?
- What controls are used with your engine package?
- What happens if I lose a serpentine belt?
- What engine functions should be monitored?
- What engine monitoring system do you recommend?
Regarding the Wheeler:
- I heard that you lost your test bed airplane. What happened?
- Bud Warren’s plans to replace the Wheeler:
- How did your PSRU fare after the fire and forced landing?
Questions Regarding PSRU for LS1 Engines
What temperature does the PSRU operate?
Our PSRU runs cool. High temp for our unit is 150 degrees F. We test run each unit for an hour each before delivery, and the highest temperature we have seen is 120 degrees F. You can expect to see higher temperatures at climb out, but once you have leveled off the temps will normalize again.
How is the PSRU lubricated?
This unit has a separate oil reservoir with its own oil pump and filtration system, lubricating all of the gears, bearings, shafts, prop hub and prop governor with clean, filtered oil as long as the prop is turning.
What type of oil is recommended?
We have tried virtually every kind of oil and gear lube on the market, including five or more major brands of synthetic gear lube. The only lubricant that has provided appropriate lubrication and cooling with quiet and smooth operation is a regular mineral type 85-140 gear lube. This will be labeled “limited slip, API service GL-5” or greater. It will generally be formulated with more or less enough anti-foaming additive to keep the gear lube from foaming up, but brands and even batches will vary. Because of this, gear lube should be checked during ground testing when the PSRU is first installed and checked to be sure it does not look grayish or cloudy in color, which means it is foaming up. Should this be the case, simply purchase “limited slip differential axle additive” from your local auto parts store, and add one ounce at a time until the gear lube runs clear. Foaming means that there is too much air in the oil and that will not allow the lubricant to film properly on the interior parts and will cause premature wear of the internal components
Never use synthetic lubricants in any of our products. This was so important to Bud that it would void your warranty with Geared Drives if you use anything other than the lubricant he recommended. Synthetics work great in auto engines (but not if you are ever going to use 100LL) but fail miserably in a gear box environment as in a PSRU. Synthetic gear lubes in this application simply did not provide adequate cooling or lubrication, and will cause high operating temperatures, gear noise, and eventual failure of the gears.
Auto PSRU’s will be performing futher testing of synthetic gear lubes in the near future to stay up to date with development and improvements in these products. If there are any changes to this policy it will be announced here and through the users group.
Return to top
How much oil does it hold?
The BW350 PSRU holds two quarts of gear lube, and the 200Z PSRU holds one quart of gear lube. If you choose to use an oil cooler, simply add the capacity of the oil cooler and the lines to the fill up volume. Use only 85-140 mineral type gear lube with anti foaming additive.
One customer is using a Kingair type prop, and this prop and hub demands so much oil volume that the only way to supply enough lubrication to the PSRU, prop and and governor is to add an oil tank for the PSRU to draw from and for the oil to return back to when the engine is off. This kind of prop will draw enough of the oil out of the PSRU that it will fail due to insufficient lubrication. If you are planning to use a prop like this feel free to contact us for more information.
Return to top
How does the prop governor work on your PSRU?
Both PSRU’s pump fresh filtered lubrication throughout the entire system supplying oil to the prop governor, prop and hub. The drive port for the governor is located on the left side of the PSRU and driven from an accessory shaft that turns off the splines on the prop shaft. The other end of the accessory shaft powers the oil pump for the PSRU.
Return to top
Will my prop governor work with your PSRU?
If your prop turns the conventional direction and your prop governor turns clockwise, it will work with our PSRU with no modifications. We have not found any particular brand of prop governor that does not work with our system. Even though we are supplying oil at 60 PSI to the prop governor, we have found that a prop governor does not require a massive quantity of oil if the governor and propeller are in good repair and are not leaking. The prop governor itself is an oil pump, so as long as it has a constant steady oil supply it will function properly. We have tested this theory by cutting down the oil flow with a 1/8″ orifice and the prop governor still worked correctly. We do not have oil temp, oil volume, or governor problems.
Return to top
Why do you use a centrifugal clutch?
The centrifugal clutch serves a number of different functions, but the primary and most important is that it serves to resolves torsional vibration by means of a set of heavy polymer coated springs in the center of the clutch disc. Since the clutch disc, flywheel and pressure plate do not constitute a hard connection, there is thought that perhaps some of the harmonic issues might be solved there as well. In addition, the centrifugal clutch engages the prop at low RPM and after the engine is already running, which could dramatically extend the life of your starter. The clutch also disengages when the engine is shut down eliminating prop “kick-back” from shaking the entire aircraft. Clutches have been used in auto engines to dampen harmonics between the engine and transmission for many years. Without a clutch in your transmission to serve this purpose, your vehicle would hop and skip down the road instead of rolling smoothly to your destination.
Return to top
My old PSRU chatters and jumps around at low RPM. Does yours?
No it does not. We tested our PSRU for literally hundreds of hours on the ground and experienced no chattering or vibrations at any RPM. Bud flew his Wheeler for nearly 700 hours with great success and no torsional vibration. Our PSRU operates smoothly at every RPM and transitions equally as smoothly from high to low RPM and everything in the middle.
Return to top
How do you resolve torsional vibrations?
Years of designing, redesigning, going back to the drawing board and starting over have yielded a PSRU which utilizes a custom designed centrifugal clutch assembly. This was designed specifically for use on an automotive engine for experimental aircraft, and incorporates a center clutch disc with polymer encased springs. This use of this disc not only makes the system work and eliminates torsional vibration, it offloads the engine long enough get it started which avoids strain on the starter. There is virtually no wear on the clutch disc since it simply engages and then disengages. The harder the engine is running, the more firm the connection.
Return to top
What about planetary gears in a PSRU?
I choose to use the best for safety and dependability in our PSRU’s. For this reason, I am against the use of planetary gears in a PSRU. Considering what they were designed for, to change an automatic transmission from one gear and into another. They were designed to work at high RPM for only short periods of service. They are very small and turn at ultra high RPM when in continuous use, and from twenty plus years of personal experience in professional auto racing, Bud’s personal opinion was that there is no way that planetary gears can possibly hold up long term. The strongest and most dependable kind of gear is a straight cut spur, which is what Bud chose to use in these PSRU’s.
Return to top
Do you test run each PSRU?
Yes. We have an early model Chevrolet LS engine that we use to test run each PSRU. For break in, we bolt on a test propeller and test run for one hour following the resolution of any leaks that might be found. This allows the seals to seat, and operating temperatures to normalize. We run the unit from 500 RPM all the way up to takeoff RPM of 3900-4500, and everything in between. We are able to cycle the prop, make many engine RPM changes, and put the engine and PSRU through the same paces that you would if you were ground testing it on your aircraft. This way, we can ship these units out knowing that all is exactly as it should be. To witness this test run is an incredible sight. The smoothness and ease of operation is really rather incredible.
Return to top
How much HP will your PSRU take?
Bud had great success with 405 HP in the 383 Chevrolet installed in his Wheeler Express for the nearly 700 hours that he flew as a test aircraft, so we can say for a fact we know that it will hold 400 HP.
Return to top
I have an electric prop. Can I use it with your PSRU?
Yes. When you place your order one of the things we require is that you indicate your prop type and bolt pattern so we can drill the prop shaft correctly. We provide a plug at no cost to you for the prop shaft to close off the hydraulic system if you are going to use your electric prop.
Return to top
Can I use a fixed pitch prop?
We have long stated that we have no restrictions on which prop you can use with our PSRU and to the largest extent that is true, however be aware of the following:
1) Fixed pitch props lack the protection of a prop governor which means there is no provision to keep the prop from “over speeding”.
2) KingAir props. These props require an inordinate volume of oil and literally suck the PSRU dry of oil. If you must use one, contact us about how to construct and plumb in an auxiliary oil tank for the PSRU to draw from and to provide a place for the oil to drain back into when the engine is shut down.
Return to top
Questions Regarding PSRU for LS1 Engines
Any plans for a PSRU for Mazda?
Yes. Our 200Z Zero Offset PSRU fits Mazda, Subaru, Corvair, VW, etc and adapts by means of a mounting plate specific to the engine. We already have several customers flying with the 200Z and have reported exceptional performance, commenting on how smooth and powerful their engines now run. They also reported cooler engine temperatures, improved climb rates and more economical fuel burn. It appears that we have built a gearbox that the Eggenfellner owners would not only be pleased to fly, but will improve their engine and aircraft performance far beyond their expectations.
Return to top
Questions Regarding FWF Engine Packages
Why build a FWF package for the RV-10?
The RV-10 is a perfect airframe for an engine such as the LS1. The LS1 and the Auto PSRU’s engine package is ideal for pretty much any application that would normally have called for an IO-540 or O-540. This engine package, ready to run with all accessories including radiator, starter, alternator, oil and water, comes in about 20 lbs less that the average IO-540. So the old myths that auto engines are so heavy is not entirely accurate when you consider the modern auto engines of today. We have developed a firewall forward package for the RV-10 that would allow the owner to basically bolt the thing on, wire it up, hang the prop, and go fly.
Return to top
How much does an LS1 engine package weigh vs. an IO-540?
The ready to fly weight of the LS1 (less prop), complete with PSRU, flywheel, engine, radiator, all accessories, including alternator and starter, water and oil, comes in just under 500#. Bud removed an IO-540 from a Glasair III and weighed it on certified aircraft scales it came in at 530# (less prop). Yes, the LS1, ready to fly, less prop, apples to apples, weighs in less than an IO-540 and has a lot more horsepower and torque.
Return to top
How does the engine RPM compare to the IO-540?
The LS1 will happily operate at higher RPM than the IO-540. What makes the difference is that the IO-540 as a reciprocating engine which has a long stroke and monstrously large, heavy pistons. The LS1 runs at a higher RPM than does the IO-540, but the rods and pistons are so very much smaller and lighter that the certified engine pistons. Put this into perspective, only one piston from out of a I0-540 weighs nearly what an entire set of LS1 pistons weighs. The lighter pistons of the LS1 in this smooth running and well balanced engine are not creating a lot of wear and tear in the engine. The LS1 engine is capable of running happily at a higher RPM with no problems at all. Chevrolet has tested these engines unmercifully and they have proven their durability again and again.
The engine RPM range that we advocate using for aircraft use is really quite mild for the LS1. We like to see takeoff RPM’s around 3900-4000, not because more is hard on the engine, but because this is all you need for awesome performance and fantastic climb rates when combined with the Auto PSRU’s PSRU and a constant speed prop. You can even go up as high as 4200-4300 RPM if you have a heavy load, and it will not hurt the engine. With the Auto PSRU’s PSRU and property set prop governor, you will not over speed the prop and you will have lots of excess power at your disposal. You will however, need to be judicious in how you apply that power. These engines have so much power that it would be easy to torque-roll the airplane if you apply it all at once.
Return to top
Thoughts on your engine packages on P-51 replicas?
We think that the P-51 is an excellent platform for a Chevy and the Auto PSRU’s PSRU. Bud met half a dozen or so fellows at OSHKOSH in 2009 with P-51 replicas and was anxious to get one in the air with a PSRU on it behind a Chevrolet. Apparently, some years back, they used to have a source of a geared redrive that they liked to use, however it did not have all of the accessory drives built in like ours does. I am told that the builder is no longer producing the PSRU, and they are looking for a supplier for a geared drive that will perform the way they need it to. Our PSRU would allow their installation to be so much more simple, would eliminate the additional accessory drives that many currently have to use, and save on weight and initial cost. There are two customers with FEW Mustangs that have taken delivery and both are making fast progress toward completing their aircraft. We will post photos and performance information as we are able to obtain it.
Return to top
How about Chevrolet engines for twins?
If you are considering two Chevrolet engines you could use marine parts in your right engine for counter rotation. It would entail a marine oil pump, camshaft, starter, possibly a few other details. The stock alternator should work just fine. This really makes sense for a twin, since you would then have no critical engine. I am sure that you could build up an early model Chevrolet engine this way, but you might check on whether you could match a late model LS1 engine with one for marine application, since we have not yet built engines for a twin. Our Auto PSRU’s PSRU works equally well for both tractor or pusher. Be advised that you will need to work out a mounting locations for radiators, develop different cowl ventilation than that required for an air cooled certified engine and custom engine mounts must be designed as well.
Return to top
How about diesel engines in aircraft?
We do not advocate the use of a diesel engine in an experimental aircraft. Our educated opinion is that the engine compression strokes are so violent that they would likely tear up the PSRU, or any other one for that matter. Our PSRU has proven to be the toughest one around and we would not put in on a diesel under any circumstances because of the engine power pulses. High compression, strong engine pulsations, etc, together with the limited altitude ceiling for a diesel do not, in our opinion, make any sense to use in aircraft, both in terms of safety and cost. The diesel also adds a huge weight penalty compared to gas powered auto engine conversions. We feel so strongly about this that we will not sell any drive of ours to anyone planning to use it on a diesel engine. We do not want to be any part of someone hurting themselves or others doing something that goes against what we know is good sound advice.
Return to top
What cooling setup do you recommend for your engine packages?
There may be variations from one airframe to another, but in general, we make the following recommendations for a tractor configuration. Whether it is a one or two radiator configuration, we want to see each with an air inlet scoop that will allow a large volume of fresh air directly through the coils of the radiator. NACA scoops look great but are mounted so they are inside the boundary layer of air around the cowl in flight and will not capture enough forced air to provide sufficient fresh air flow. Cowl side inlet scoops reach out beyond the quiet boundary layer of air and grab air from off the prop and it is then forced through the radiators. These air inlet scoops should have approximately the same air volume as the front inlets on the cowl. When you add side cowl scoops, you must now block off the front air inlets altogether as they will inhibit the high pressure zone you are trying to set up. Then supply a fresh air inlet approximately 3-4 square inches in size just underneath the spinner to provide air to the PSRU. Combine all of that with 1.5 to 2.0 times the square inches of exit air as you have cowl side scoop and your engine will run cool. This has never failed us. If it designed correctly there will be no need for fans on the radiators.
Return to top
What about baffling?
You will only need to baffle between the radiator and the cowl. The baffles should be relatively close and tight but are not extremely critical; even if you were to lose five percent of the air around the baffle it will not adversely effect the cooling due to the sheer volume of air that will be introduced through the cowl from the side cowl scoops We are also against ducting air from the front air inlets to the radiators inside the cowl because it doesn’t maximize air circulation to the radiators, and the ducts block the cool air from circulating around the engine.
Return to top
Did you say close off the front air inlets?
We do not recommend you rely on the front air inlets to supply enough fresh air to cool the engine and cool the water in the radiator. This is because there is not enough air through the front inlets alone to sufficiently cool a V8. The reason there is not a large volume of air generated through the cowl from the front air inlets on most aircraft is because the propeller is generally rounded at the root and does not move air like the airfoil part does. This being the case, we prefer to go to the side of the cowl and capture the air we need to achieve cooling.
Return to top
What about drag?
We are aware that many builders are resistant to side cowl scoops because they think that the “drag” will slow them down, and they don’t want to change the look of the airplane. Consider this: our engine packages out perform anything else out there and we don’t think you would ever notice any “drag” because the Chevy can outrun anyone anyway. Number two, if you have to live with what you consider to be a little “drag” what does it matter if the engine is cool and happy, and you are burning 30% less fuel anyway? Cooling is a requirement. We have forged the way to cooling correctly, at least a way that works for us every time, in every airframe. Those who take our advice will find it works. We like to keep things simple.
Example One: The Ravin 500 with LS1 and side cowl scoops vs. the Ravin with IO-540 and conventional front air inlets…the LS1 Ravin with side cowl scoops out climbs and out runs the IO-540 Ravin hands down.
Example Two: Bud’s fixed gear Wheeler Express would climb out 4,000 FPM and was perhaps the fastest Wheeler in the world, and it flew with two side cowl scoops and blocked off front air inlets. A retractable gear Wheeler is 30 KTS slower!
When you can fly an airplane in smooth air to Vne at will with one of our engines, then it is easy to see that drag from the side cowl scoops is not an issue.
Return to top
What controls are used with your engine package?
You will use a key or push button to start, and your prop adjustment. That’s it. There is no fuel mixture since ECU makes those adjustments automatically.
Return to topp
What happens if you lose a serpentine belt?
We love the dependability of the LS engines, but in the back of our mind it is hard not to think about what would happen if we ever lost a serpentine belt. The primary issue is how to keep the engine from overheating with the loss of the water pump function. The answer is to install a water pump inline as a booster between the mechanical water pump and the radiator. We have found one that we like from Stewart Components, that is small, relatively light weight and easy to install. When not in use the water flows through, but when you find you need it just switch it on and it will keep the engine cool (might even reduce the temperature since it circulates 300% more volume) and will certainly give you plenty of time to find a place to land. (Since this pump greatly reduces dwell time in the radiator, it should not be used as a primary pump).
The second issue with loss of a serpentine belt is that the alternator will no longer charge the batteries. We always recommend that you use a two battery system with each battery on a separate switch. Use both for take off and climb out, then switch one off at altitude so you always have a battery in reserve. A battery in good condition and fully charged can give you thirty to forty-five minutes of flight time, but certainly enough to get you to the nearest safe place to land.
Return to top
What engine functions should be monitored?
We recommend that you monitor engine oil temperature, oil pressure, engine water temperature, gearbox temperature, and gearbox oil pressure. We also recommend that you use automotive type gauges as a back up to your monitoring system. We have found that some customers do not have the correct sensors for their engine monitoring system, and the results are off the wall crazy readings. If your readings seem off, verify that your electronic sensors are reading properly by checking against a mechanical automotive type gauge. For temp sensors, test by placing it in boiling water and verify 212 ̊ F readings. Contact your engine monitoring system vendor if you have any issues with incorrect readings.
Return to top
What engine monitoring system do you recommend?
You may use any engine monitoring system you desire. It can be as simple as automotive type gauges on your panel if you are from the old school, or as elaborate as a glass panel if you like. Each builder has to determine his preferences in this way. There are many different systems from which to choose, so as part of your due diligence, be sure that the system you are contemplating supports the V8 auto engine. This means that some will have to install the correct sensors within the instrumentation, or change some of the calibrations in order for your readings to be correct. Incorrect sensors or calibrations will result in unrealistic readings, such as engine oil pressures of 85-100 psi etc.
Return to top
Questions Regarding the Wheeler
I heard you lost your test bed aircraft. What happened?
Bud was flying to West Houston Airport in his Wheeler, to an EAA chapter meeting where he was invited to speak. He had taken off only a few minutes prior, and the flight was proceeding as planned. Perhaps ten miles from CXO he noticed that the engine oil temp was getting higher. The water temp was fine, oil pressure was fine, and then the engine coughed. Just a moment later there was smoke in the cockpit and he asked his passengers to help him find a place to land because they were going down. Losing power quickly Bud did a 360 in the air and saw a hay field in the distance, the engine quit just before they made contact with the ground, and they hit a couple of posts in the fence, taking out the left wing, which sent the airplane into a spin on the freshly mowed hay field. The impact forced the landing gear up through the wings and they were spinning on the belly and seeing nothing but fire all around, but once they got on the ground and the airplane came to a stop, they were able to escape the aircraft through the passenger door.
They stood and watched helplessly as the aircraft burned to the ground. Bud had minor burns on his fingers from the seatbelt clasp which had already heated up enough to burn him, and a couple of nice goose eggs on the top of his head. James bruised his ribs and received a slight flash burn on his face, and Bud’s daughter, Phyllis skinned her elbow on the wing tread escaping the aircraft. They were very grateful to be alive, but heart sick at the same time as the magnitude of the loss began to sink in. They had lost the Wheeler.
Investigation proved that the source of the engine fire was a braided steel fuel line which failed. This caused fuel to spray over the exhaust on the right hand side of the engine, which burned the distributor cap and spark plug wires off of the engine. The cough they first felt was the first symptom of the ignition system burning. Apparently the oil temperature sensor heating up from the fire is why they were getting a high engine temperature reading.
Return to top
Plans to replace the Wheeler demonstrator:
Bud never replaced his original Wheeler, but interestingly I have a very similar Wheeler under construction in my shop. Obviously it will have an LS engine and BW350 installed in it.
Business is such that we must focus all of our time and energy on completing the transition and start up of Auto PSRU’s from the remains of Geared Drives. So far the focus has been to get suppliers up and producing parts for us again, and supporting legacy customers with the parts they need to correct in service issues. There is a backlog of potential customers interested in placing new orders for both gear boxes. Once the flow of parts is going again orders and deposits will be accepted. To take deposit money before that would be unethical. When this milestone of progress is reached it will be announced through the users group and on the NEWS page of this website.
Return to top
How did the PSRU fare after the fire and forced landing?
Bud salvaged the 383 engine and Geared Drives PSRU from the fire and disassembled them to see how they fared from the impact and engine fire. The engine had lost power due to the fire taking out the electrical system so the prop was just wind-milling when they touched down, but even so, he was humbled to find that the PSRU was totally undamaged. Bud mic’d the prop shaft and found it to be within .001 of its original dimension. There was no damage to bearings, bearing surfaces, shafts, or even the PSRU case.
Return to top